Over the last fifty years or so, irrigation techniques have just got better and better at improving irrigation efficiency, which is a measure of the relationship between the results obtained and the resources used. Localised irrigation (drip irrigation, micro-aspersion), which can be defined as the application of a very limited volume of water that matches the plant’s requirements as closely as possible, is now considered to be the most suitable technique available for achieving this irrigation efficiency.
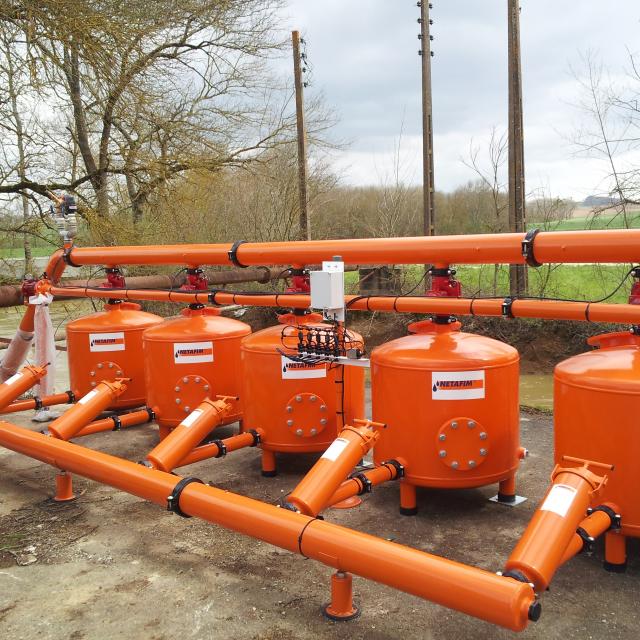
Thus, this technology allows the users to strive towards achieving the best form of irrigation, operating almost continuously with very low-flow emitters (often less than 0.6 1/h), while respecting the balance of the soil (minimum percolation and keeping the water in the rooting system, minimal soil compaction…) and helping to achieve an ideal agronomic solution. This water is increasingly becoming the carrier of nutritive substances (fertilisers), allowing the quantity used to be restricted while maximising the impact (precise localisation of the application). However, inevitably these systems require the very best filtration methods, capable of effectively protecting these innovative irrigation systems from particles that might clog up the equipment (sediments contained in the water or residues of poorly diluted nutrients in the water).
Monitoring the developments in filter technology
We work with the best manufacturers in the world so as to be able to identify, offer and develop effective filtration systems, for many possible uses, bearing in mind the many limitations existing in the field (economic constraints, limited available space, variable labour quality…). There is also the problem that an ever scarcer resource can contain particulate solids: water quality now tending to drop worldwide.
Existing filter technologies
With existing technologies, we must firstly mention the oldest of them all, that of sand filtration. This was already being used by the Romans in ancient times to filter water used for human consumption! It consisted of allowing untreated water to pass through a bed of filtering material at a slow speed (0.1 to 0.2 m/h), such as sand, for example. A part of the suspended material particles (minerals or vegetables) will be trapped while the water quality will improve as it passes through the medium. It should be mentioned that filtration efficiency is clearly linked to the form and type of materials in suspension (size and shape of the suspended particles that determine the most efficient pore size required for trapping the particles) as well as the flow rate of the water passing through the filter (the slower the flow rate the more efficient the filtration). It can, therefore, be stated that economically the optimum for filtration in agriculture has been defined as an average flow rate of between 40 and 60 metres per hour with a sand particle size of 0.8 to 1.2 mm.
More recently, the screen filter has appeared on the scene, consisting of a woven stainless steel mesh that forms a barrier capable of retaining the solid particles (the filter element). The distance between the wires will determine the orifice/filter mesh size. The water containing the suspended particles will flow through these orifices, with the larger sized particles being held back by the woven wire mesh. We, therefore, refer to the fineness of the filter screen: a mesh of 130 microns (average retention value required for protecting localised irrigation systems of the drip type) will “on average” only allow smaller sized particles to pass through, which will not damage the system downstream (irrigation system with emitters). However, we must not forget that the particles contained in the irrigation water can be of infinite shapes and forms, not always capable of being easily blocked by a screen. For example, filamentary algae can, within a certain limit, manage to slip through a screen by being carried along with the flow. Thus, even though this form of filtration offers a number of advantages (as we will see below in the case of compactness, in particular), we can conclude at this stage that it will be less efficient in absolute terms than a traditional sand filtration method.
The latest method to arrive on the agricultural market and certainly the most promising is disk filter technology, which without doubt is the system that perfectly combines the advantages of the previous two technologies. This consists of a stack of grooved disks through which the water will circulate. The diagonal grooves, calibrated according to a specific level of filtration, are criss-crossed in the stack, thus reproducing the succession of cavities or traps found in sand filter technology to increase the possibilities of holding back the particles present in the irrigation water. In the same way, if the particles are not of the optimum shape and form, they can still be effectively blocked by a device that resembles an infinite number of super imposed screens. With this compact and efficient solution it would appear that a difficult problem has been resolved.
How to make the right choice with so many types on offer ?
So does this mean that a disk filter should always be the technology to use when looking to set up a localised irrigation system? In our experience, we would be tempted to say yes, but this would be without taking into account the actual financial constraints imposed by some customers or their trepidation about blockages and other problems that may arise with these innovative solutions. That is why we are promoting three kinds of technology! Incidentally this will also enable us to be more aware of the restraints, constraints and apprehensions of certain clients and be able to respond with a certain degree of conservatism.
A field study needs to be carried out
So what can we do in the field? Firstly we need to identify any constraints and the precise customer requirements. What is the water source (surface water liable to accumulate particles when the water level rises or during very windy periods, water from depths still affected by surface turbulance)? How is this resource pumped (use of a strainer as the first barrier, positioning the suction pipe between the two water levels or on a floating system, suction intake in the direction of the wind…) and what is the end use of the filtered water (the requirements are not the same for an above-ground microsprinkler with a flow rate of 200 l/h as they are for a subsurface drip irrigation system of 0.6 l/h per emitter)? What volume is available for the installation of a filtration system? Is the customer opposed to the proposal of a plastic product? Has a water analysis been carried out during the most difficult period so an attempt can be made to identify the type and significance of the particles in suspension (concentration of materials in suspension in mg/l, mineral or organic type, particle size distribution), Biological Oxygen Demand which typifies the level of pollution of a biological type that is often difficult to prevent)? Is there a willingness and capacity to invest in a product provided with an automatic back-flushing system, capable of regenerating the filtration capacity after a change in the differential pressure specification of the filters and are there any filter clogging images available?
A solution that should meet the demand and needs of the customer
With this client information we are able to propose different solutions, putting forward the advantages and disadvantages of all these solutions, while still leaving the client with the freedom to make the final choice.
Using a purely safety-first approach in the case of an existing primary filtration system, we are able to offer manual filters with a metal body and stainless steel screen or a plastic body and stainless steel technology or plastic disks. With these manual filters, the irrigation will have to be stopped for manual cleaning, but the frequency of maintenance will be restricted by their positioning down stream of the primary filter. They will be placed as close as possible to the emitters (in the area to be irrigated), which, as an analogy, is similar to the way a fuse protects an electrical appliance.
For the configuration of a primary filter, generally speaking the filter station is placed as closely as possible to the water source and upstream of the whole irrigation water supply circuit. We provide a wide range of automatic filters with metal bodies of the sand type (sand filter station) or screen type, or even automatic filters with plastic bodies of the disk type (“Spin Klin” filter station). The most economic of these is the screen filter technology, closely followed by the disk method, with the traditional sand solution following on from these, this in itself being handicapped by its volumetric limitations (at least two to three times more surface area is required on the ground to install an automatic sand system compared with the automatic screen and disk products.
For the most demanding users, it will also be necessary to take into account the back-flushing of sand filters: requiring a far higher instantaneous flow rate than the less thirsty automatic screen or disk solutions (a ratio that could be as high as 4 or 5).
Conclusions
Choosing a suitable filter is not an exact science! For this, we use experience and a detailed analysis of the demand. This cannot be achieved without a certain dialogue with the client who will, of course, be the end user responsible for maintenance and monitoring in the field. And that is why it is important for this user to be fully at ease with the chosen concept! It must not be forgotten that automation has been the main advance in the development of filtration systems: this evolution being based on the latest technology in screen filters (simple and compact), sand technology (efficient, even in very contaminated water, but very demanding on water and space) or disk technology (the best compromise), this automation process going one step further to the point where it can now be used with all existing methods… providing they have been designed in an appropriate and professional manner !