A device that is well-designed and adjusted can save water and improve yields.
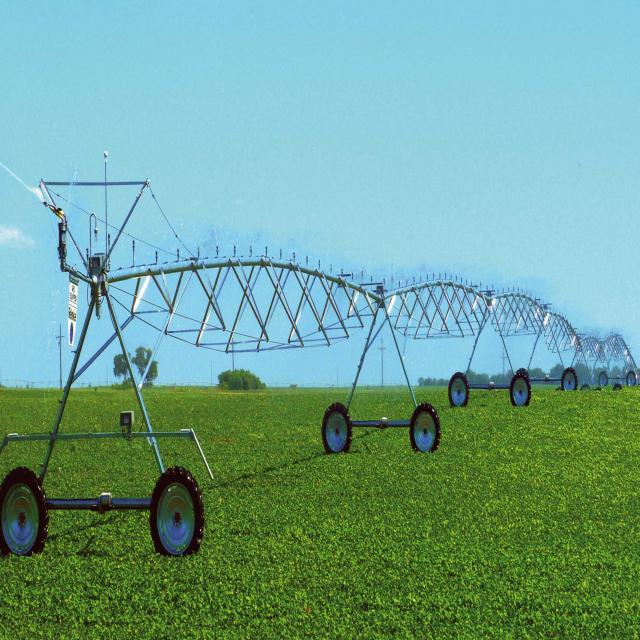
How to select and use a pivot ?
• Design criteria.
The daily amount to be applied (mm/day) determines the flow rate required by the equipment. This amount depends on the soil water holding capacity and its infiltration rate, as well as the crop water requirements and the amount of any possible rainfall during the irrigation season. In an existing installation, knowing the pressure and flow-rate of the pump will determine the size of the machine and type of sprinklers. The throw or range of the sprinklers determines the intensity of the precipitation rate.
• Selection criteria.
- Choosing the sprinklers according to the available pressure: the pivot’s sprinklers should be low-angled and operate within the pressure range for which they were designed (see table below).
- Influence of wind drift: sprinkling is even more sensitive to wind drift when the spray consists of small droplets (particularly in the case of high pressure or when the nozzles are positioned high above the ground).
- Sprinkling intensity: the weaker the throw of the sprinklers, the greater the intensity. Combined with the droplet size, it is directly responsible for damaging the field surface if it is not adapted to the type of soil: risk of compaction and the resulting runoff.
- Comments: it is often necessary for pressure regulators to be fitted on the sprinklers in difficult areas. The manufacturers should respect the European standards currently in force.
3 EN 12325: description of the installations, minimum performances and technical specifications (nozzle package).
3 EN 909: complying with the safety requirements of the pivot and lateral move type installations.
All of this information is reflected in the chosen nozzle package plan, which incorporates most of the data listed above. This is a contractual document and must be sent to the irrigation operator.
Using the devices
At the very start of the campaign
• Drain the system
• Check: that the sprinklers are functioning properly (rotation, obstruction) and that the pivot end gun is properly adjusted (range and angle of the sprinkler spray as specified in the nozzle configuration plan).
The pivot end gun can cover up to 25% of the surface area to be irrigated, depending on the size of the machine. Its pressure should allow for an efficient range of throw, generally ¾ of the normal range. The uniformity of irrigation at the end span depends on the proper adjustment of the angle of the arc.
• Check the pressures with a portable pressure gauge at the first and last span. These pressures should conform to those specified in the nozzle configuration plan (do not leave the pressure gauge permanently connected to the installation).
• Check that the spans are in line (with each other).
During the season
The nozzles and the sprinklers have an average life span of 5 to 10 years.
• Check the pressures at the pivot point and at the furthest span. If the pressures differ from those prescribed, the flow rate will be different and so the amount applied and the water distribution will be poor. These measures should be carried out regularly and they are essential in the case of a change of nozzle package.
• Check that the sprinklers and pivot end gun are functioning properly (rotation, obstruction, end gun shutoff device)
• Calculate the amount applied. This can be determined by using the following formula:
D= Q x 2n x R
S V x 10
where,
Q is the flow rate at the intake of the device (in m3/h)
S: is the surface area irrigated (ha)
V: is the average forward speed of the last tower (m/h)
R: is the distance between the rotation axis
and the last wheel (m)
TT = 3.1416
In the case of a device operating in reverse, correct S and R only, without forgetting to note the time required for the machine to return. For an end gun that functions intermittently, only correct S.
At the end of the season
• Grease the transmission
• Pump up the tyres to avoid creasing
• Protect the electric installations
Having an efficient irrigation machine means that the correct amount of water is applied. It should take into account the soil characteristics (storage, permeability) and the precipitation rate of the irrigation system, allowing the crop water requirements to be met during the periods of peak demand.
Rapid test to ensure that the device is properly adjusted
• Checking the amount of irrigation water applied.
This check can be carried out by placing containers (trays) under each span at an identical distance from each tower (e.g. 15 m). This test can be conducted several times. If the results of the measurements show a difference in the amounts applied of more than 20%, then a complete diagnosis will be required.
If the variation produces a dosage error of 10%, this could lead to a yield loss of 20% in light sandy-type soils. If the under-dosage of one span should be translated into the application of extra water cycles, then there will be an over-dosage on the remainder of the field resulting in water wastage.
• Checking the pressure of the end span
It is quite simple to check the pressure at the end sprinkler (using a tapping clip or branch stub).
If the pressure is found to differ from that of the nozzle configuration plan, then firstly check the pressure at the intake then the pumping station.
In the event of a significant variation in pressure between the pivot intake (at the first span) and the end span, then it is recommended that the device should be drained to ensure that there is no clogging. If the problem persists, then the nozzles must be changed.
• Checking the installation’s flow rate.
This check can be made by gauging the level in the water collection tank or by using a volumetric flow counter. A measurement is taken with an ultrasonic flow meter when carrying out a complete diagnosis of the device.
• Carrying out a diagnosis of the hydraulics
This allows for a check to be made of the flow rate at the device’s intake, the pressure at the pivot point and then at the end. If the pressures are found to differ from those prescribed by the manufacturer, then it will be necessary to look into the cause and also consider the possibility of designing a new nozzle configuration plan adapted to the existing hydraulic properties of the soil.